Setting the fuel level in the carburetor float chamber 21051-1107010
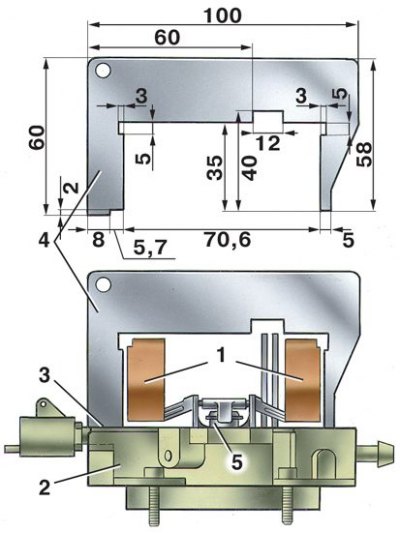
1 - float; 2 - carburetor cover; 3 - gasket; 4 - caliber; 5 - needle valve
Setting the fuel level in the float chamber
The required level is ensured by the correct installation of serviceable elements of the locking device.
The correctness of the installation of the float 1 is checked by gauge 4, for which it is installed perpendicular to the cover 2 with the gasket 3, which must be held horizontally with the floats up.
Trigger Adjustment
When turning lever 4 (see fig. Carburetor starter 21051-1107010) control of the air damper 5 fully counterclockwise, the air damper must be fully closed under the action of the spring 7. If the damper is not closed, eliminate the cause of jamming.
With the air damper fully closed, press manually on the rod 3 of the starting device until it stops. In this case, the air damper 5 should open by 3.0 mm (starting clearance B). If necessary, adjust the gap with screw 2.
Throttle valve 12 of the first chamber with a fully closed air damper should be ajar by 1.1 mm (starting gap C). Adjust this gap with screw 10.
Carburetor idle adjustment screws 21051-1107010
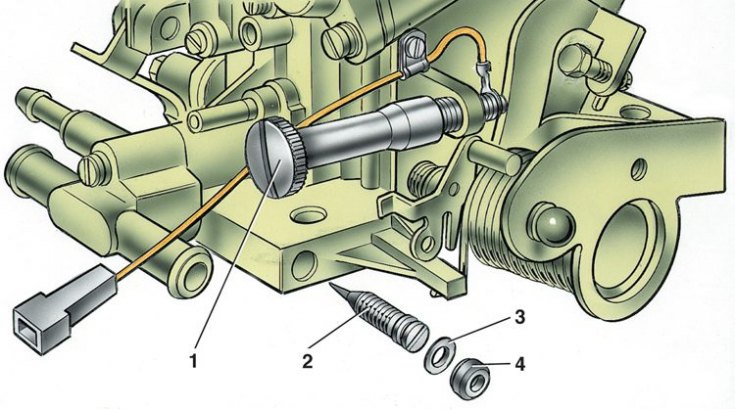
1 - adjusting screw for the amount of the mixture; 2 - quality adjusting screw (composition) mixtures; 3 - sealing ring; 4 – plug of the adjusting screw
Engine idle adjustment
Idle adjustment elements include quality 2 adjusting screw (composition) mixture and adjusting screw 1 of the mixture amount. The adjusting screw 2 is closed with a plug 4. To access the screw it is necessary to break the plug.
Idle speed adjustment must be carried out on a warm engine (coolant temperature 90–95°C) with adjusted gaps in the gas distribution mechanism, with a correctly set ignition timing and with a fully open air damper.
1. Using the adjusting screw 1 of the amount of the mixture, set the engine crankshaft speed on the tachometer of the stand within 750–800 min–1.
2. Adjusting screw 2 quality (composition) mix to achieve a concentration of carbon monoxide (SO) in exhaust gases within 0.5–1.2%, reduced to 20°С) and 760 mm Hg. Art., at a given position of the screw 1.
3. Screw 1 restore the crankshaft speed to 750–800 min–1.
4. If necessary, use the adjusting screw 2 to restore the CO concentration to 0.5–1.2%.
5. At the end of the adjustment, sharply press the throttle pedal and release it, the engine should increase the crankshaft speed without interruption, and when it decreases, it should not stall. In case of stopping the engine with screw 1, increase the engine crankshaft speed within 750–800 min–1.
6. Install a plastic plug 4 into the hole for adjusting screw 2 of the mixture quality.