Попередження! Головку блоку циліндрів замінюють з корпусами підшипників у зборі, оскільки вони обробляються разом.
Вам знадобляться: ключі «на 13», «на 17», «на 21», свічковий ключ, викрутка, круглогубці (пінцет), пристрій для стиснення клапанних пружин.
1. Зніміть головку блоку циліндрів (див. «Заміна прокладання головки блоку циліндрів»).
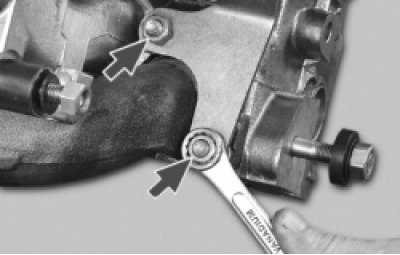
2. Відкрутіть дві гайки кріплення та зніміть рим.
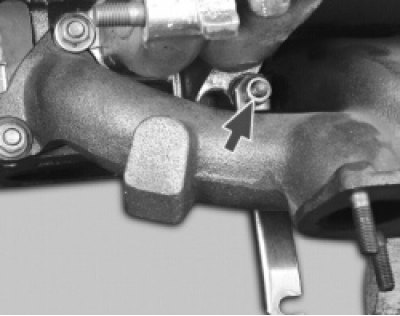
3. Відкрутіть гайку кріплення на один-два обороти і зніміть кронштейн підвідної труби водяного насоса.
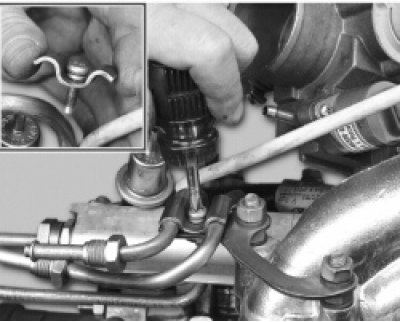
4. Викрутіть гвинт кріплення тримача паливних трубок та зніміть тримач.
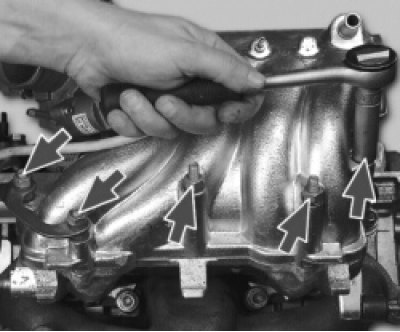
5. Відкрутіть три гайки кріплення ресивера та дві гайки кріплення кронштейна паливних трубок.
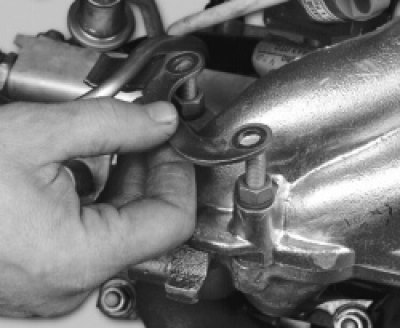
6. Зніміть кронштейн трубок.
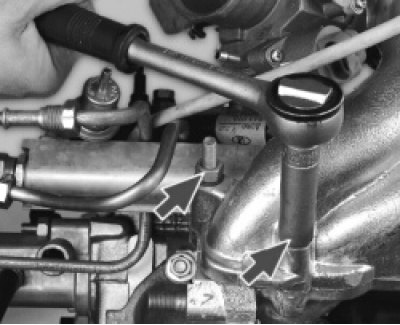
7. Відкрутіть дві гайки кріплення ресивера, що залишилися.
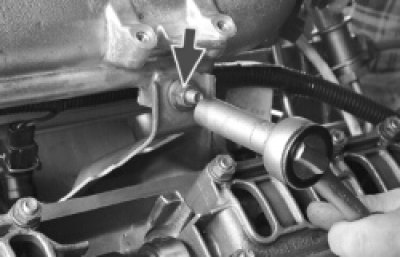
8. Ослабте затягування гайки кріплення кронштейна ресивера.
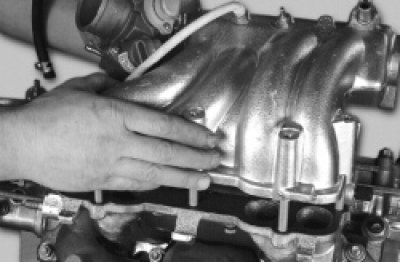
9. Зніміть ресивер.
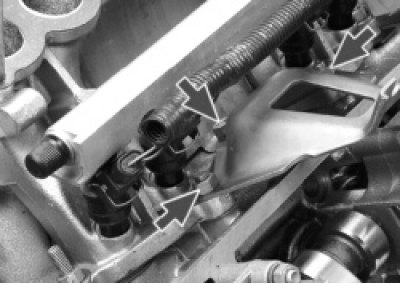
10. Відкрутіть три гайки кріплення кронштейна ресивера та зніміть кронштейн.
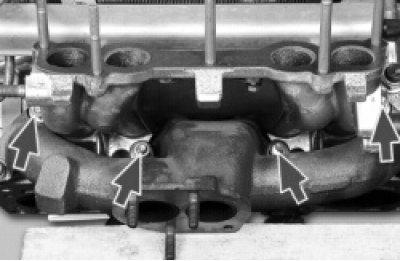
11. Викрутіть чотири гайки кріплення впускної труби.
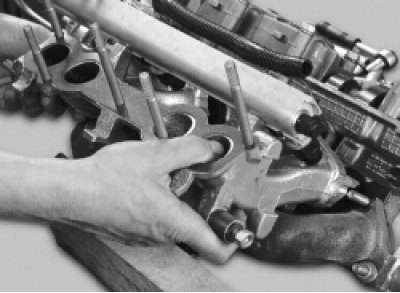
12. Зніміть впускну трубу.
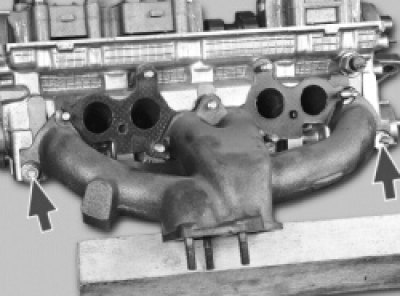
13. Відкрутіть дві гайки кріплення колектора та зніміть колектор.
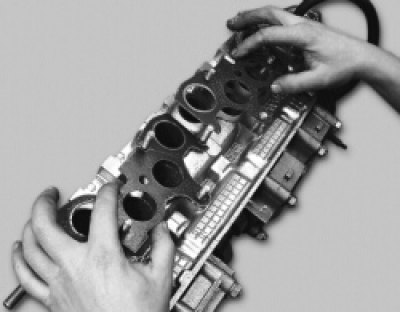
14. Обережно зніміть дві прокладки впускної труби та випускного колектора.
Корисна порада. Навіть якщо прокладки не пошкоджені і не сильно обтиснуті, їх краще замінити і не використовувати повторно.
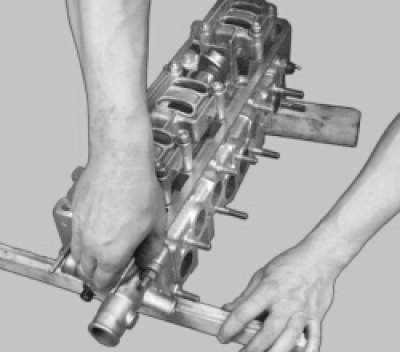
15. Встановіть головку блоку циліндрів корпусами підшипників вгору, підклавши дерев'яні прокладки під неї, щоб не пошкодити клапани.
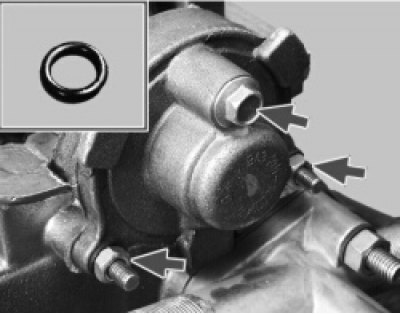
16. Відкрутіть дві гайки та болт кріплення задньої кришки головки блоку та зніміть кришку. Зверніть увагу на те, що під головкою болта встановлено кільце ущільнювача.
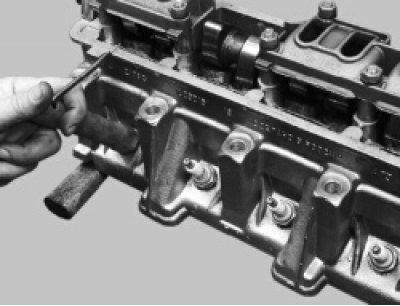
17. Викрутіть свічки запалювання.
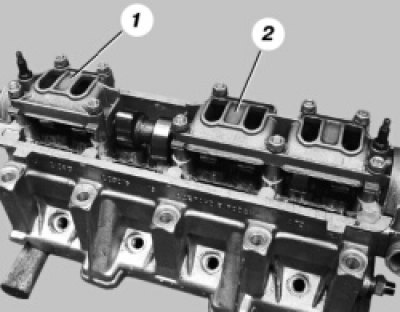
18. Поверніть рівномірно чотири гайки кріплення переднього 1 та шість гайок кріплення заднього 2 корпусів підшипників розподільчого валу та зніміть шайби. Потім зніміть обидва корпуси.
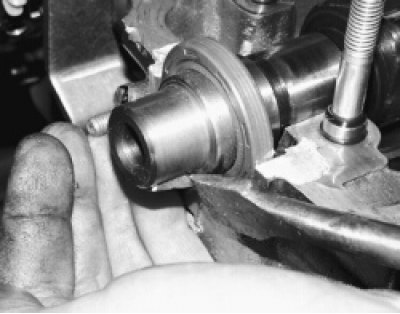
19. Якщо шпонка в пазу розподільного валу сидить нещільно, вийміть її, щоб не втратити.
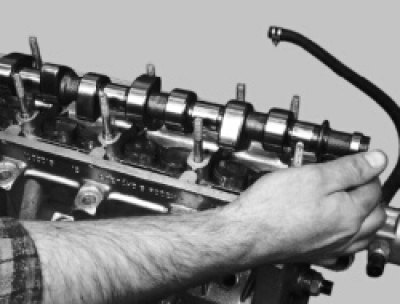
20. Зніміть розподільний вал із головки блоку.
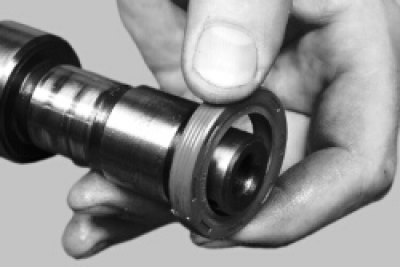
21. Зніміть сальник із розподільчого валу.
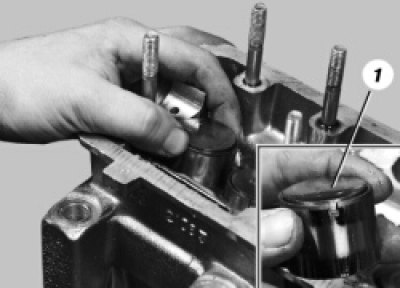
22. Вийміть штовхачі клапанів разом із регулювальними шайбами.
Попередження! Вийнявши черговий штовхач, промаркуйте його та регулювальну шайбу порядковим номером, щоб при складанні встановити їх на свої місця. Без необхідності не виймайте шайби з штовхачів, щоб не переплутати їх.
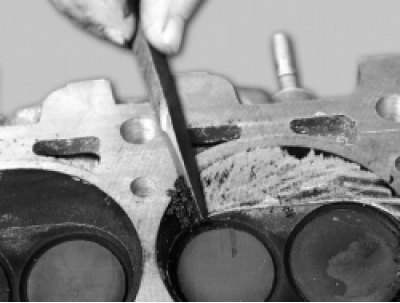
23. Очистіть камери згоряння від нагару. Огляньте голівку блоку. Якщо на ній є тріщини або сліди прогару в камерах згоряння, замініть головку. Заберіть задирки та вибоїни на площині головки блоку.
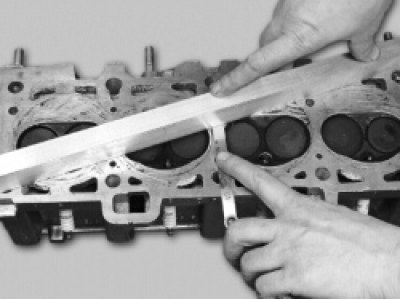
24. Перевірте площину поверхні, що прилягає до блоку циліндрів. Для цього поставте лінійку рубом на поверхню головки спочатку посередині вздовж, а потім по діагоналях і щупом виміряйте проміжок між площиною головки і лінійки. Замініть головку, якщо зазор перевищить 0,1 мм.
25. Для перевірки герметичності головки блоку відверніть дві гайки кріплення, зніміть випускний патрубок системи охолодження.
26. Заглушіть отвір у головці блоку під випускний патрубок. Це можна зробити, наприклад, встановивши глуху прокладку із щільного картону під патрубок та загорнувши гайки його кріплення.
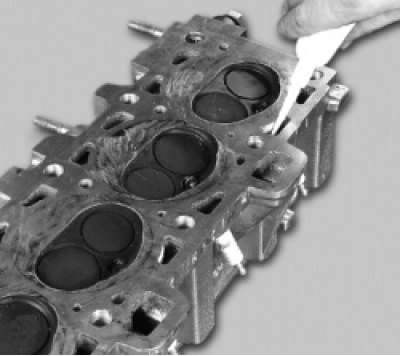
27. Залийте гас у канали водяної сорочки. Якщо рівень гасу знижується, значить, у голівці є тріщини і її треба замінити. Після перевірки не забудьте зняти картонну прокладку.
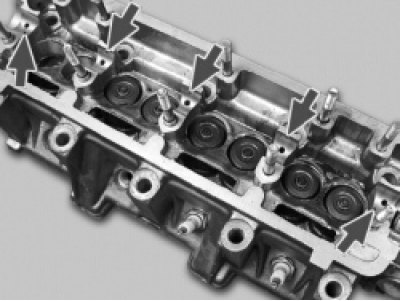
28. Перевірте стан опорних поверхонь під шийки валу на головці блоку та корпусах підшипників. Якщо хоча б на одній з них є сліди зношування, задираки або глибокі ризики, замініть головку та корпуси підшипників.
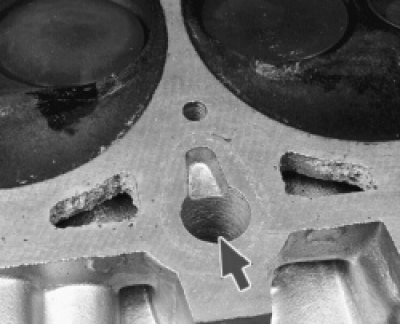
29. Промийте масляні канали. Для цього заглушіть вертикальний масляний канал із боку камери згоряння (канал знаходиться між 3-м та 4-м циліндрами) …
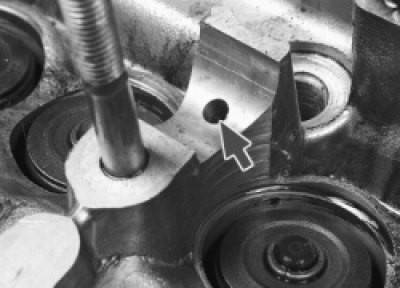
30. Залийте бензин в масляні канали у всіх опорах розподільного валу і витримайте 15-20 хв. Вилийте бензин, вийміть заглушку та остаточно промийте канали бензином за допомогою груші.
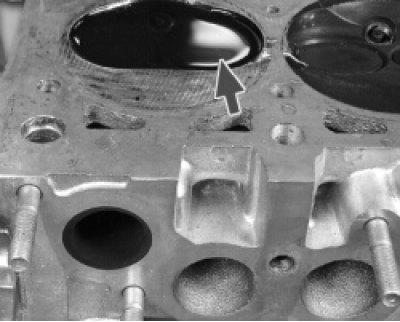
31. Для перевірки герметичності клапанів залийте гас у камери згоряння. Якщо протягом 3 хв. гас не просочиться з камер згоряння, клапани герметичні. В іншому випадку притріть (див. «Притирання клапанів») або замініть клапани.
Примітка. Привід клапанів складається з наступних деталей:
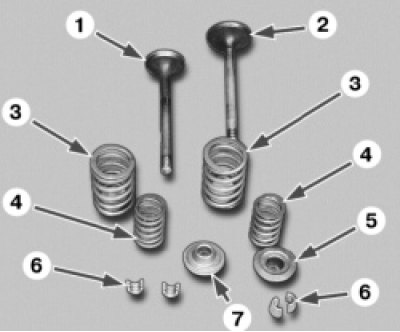
1, 2 - клапани; 3 - зовнішня пружина; 4 - внутрішня пружина; 5 - верхня тарілка; 6 - сухар; 7 - нижня тарілка. Для заміни або притирання клапанів всі деталі необхідно зняти з головки блоку циліндрів.
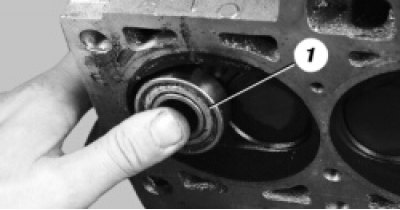
32. Встановіть під клапан, що знімається, відповідний упор, наприклад підшипник 1.
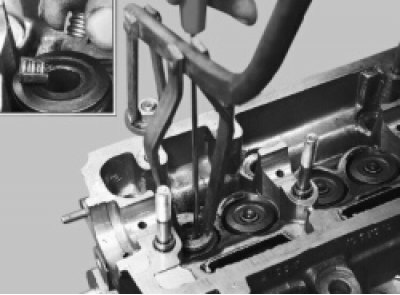
33. Встановіть пристрій для стиснення пружин клапанів та стисніть пружини клапана. Вийміть за допомогою викрутки або пінцета два сухарі.
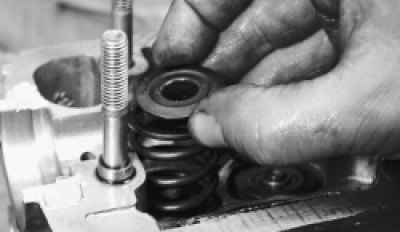
34. Вийміть верхню тарілку пружини, зовнішню та внутрішню пружини клапана. Аналогічно вийміть сухарі, тарілки та пружини інших клапанів.
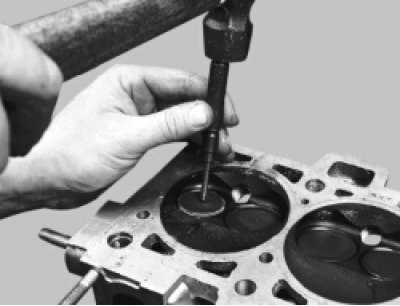
35. Промаркуйте клапани номерами циліндрів, наприклад, накерніть.
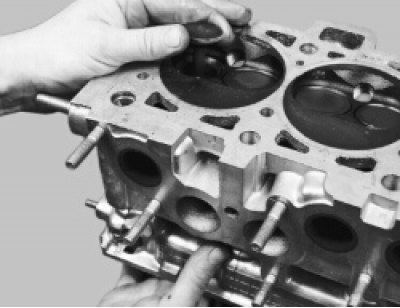
36. Підштовхнувши клапани знизу, вийміть їх із головки блоку.
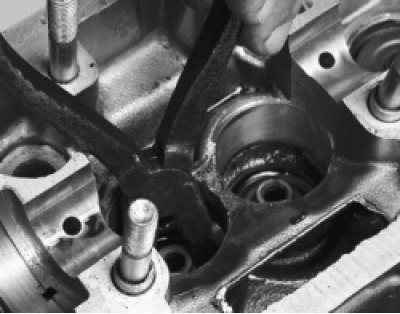
37. Зніміть олійні ковпачки пристроєм або пасатижами (див. «Заміна маслознімних ковпачків»).
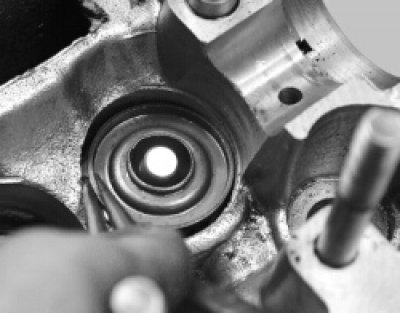
38. Зніміть нижні пластини пружин клапанів.
39. Очистіть нагар із клапанів відповідним інструментом (наприклад, металевою щіткою). Потім уважно огляньте клапани.
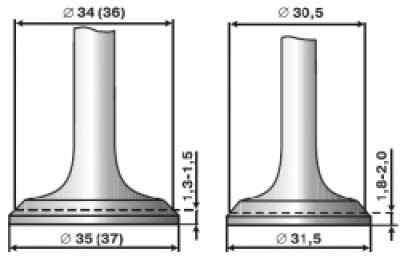
4.8. Розміри тарілок клапанів
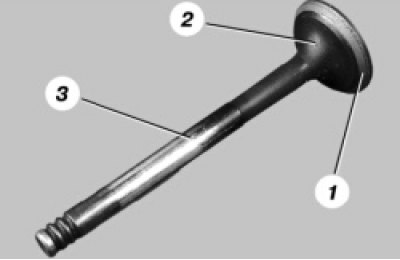
40. Замініть клапани з наступними дефектами: глибокі ризики та подряпини на робочій фасці 1, тріщини, деформація стрижня 3 клапана, короблення тарілки 2 клапани, сліди прогару. Неглибокі ризики та подряпини на робочій фасці можна вивести притиранням клапанів (див. «Притирання клапанів»).
41. У спеціалізованій майстерні робочу фаску клапанів з пошкодженнями, які неможливо вивести притиранням, можна прошліфувати на спеціальному верстаті. При шліфуванні треба витримати розміри, вказані на рис. 4.8.
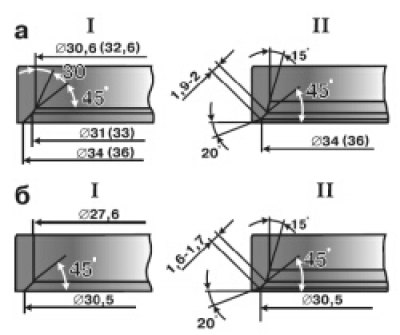
4.9. Розміри сідел клапанів: а - сідло впускного клапана; б - сідло випускного клапана; I - нове село; II - сідло після ремонту
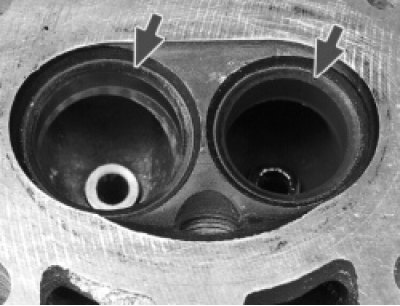
42. Перевірте стан сідел клапанів. На робочих фасках сідел не повинно бути слідів зношування, раковин, корозії тощо. Сідла клапанів можна замінити у спеціалізованій майстерні.
Незначні ушкодження (дрібні ризики, подряпини) можна видалити притирання клапанів (див. «Притирання клапанів»).
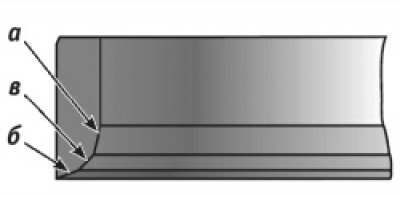
4.10. Місця обробки фасок сідел клапанів
43. Більш значні дефекти сідел клапанів усуваються шліфуванням. Під час шліфування витримайте розміри, вказані на рис. 4.9. Сідла рекомендується шліфувати у спеціалізованій майстерні.
44. Маючи слюсарну навичку, можна зробити це вручну за допомогою набору спеціальних фрез.
Спочатку обробляється фаска а (Мал. 4.10) під кутом 15°, потім фаска б під кутом 20°і фаска під кутом 45°. Після шліфування необхідно притерти клапани (див. «Притирання клапанів»).
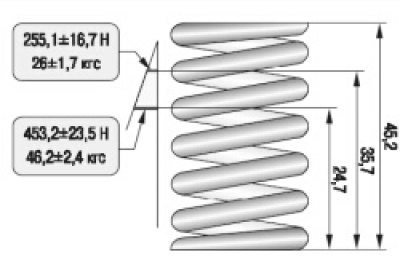
4.11. Параметри перевірки зовнішньої пружини
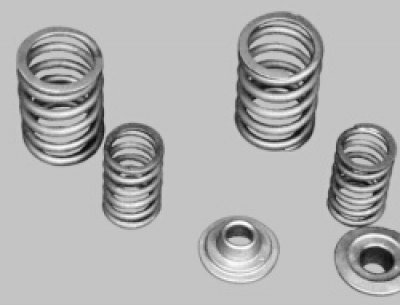
45. Перевірте стан зовнішньої та внутрішньої пружин клапанів. Замініть пружини викривлені, поламані або з тріщинами.
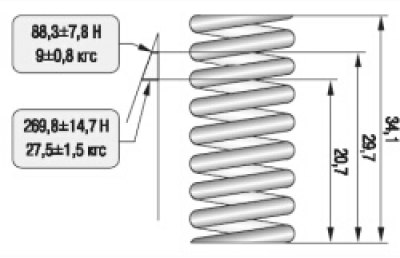
46. Для перевірки пружності зовнішньої пружини виміряйте її висоту у вільному стані (Мал. 4.11), а потім під двома різними навантаженнями. Якщо пружина не відповідає потрібним параметрам, замініть її.
47. Для перевірки пружності внутрішньої пружини виміряйте її висоту у вільному стані, а потім під двома різними навантаженнями (Мал. 4.12). Якщо пружина не відповідає потрібним параметрам, замініть її.
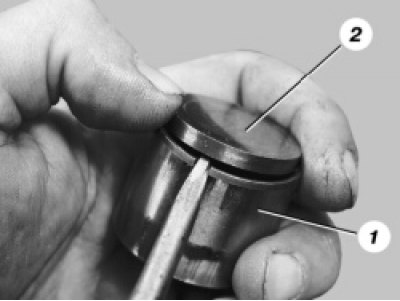
48. Огляньте штовхачі клапанів. Якщо на робочій поверхні 1 штовхача є задираки, подряпини тощо, замініть штовхачі. На робочих поверхнях шайб регулювальних 2 не повинно бути задирів, вибоїн, подряпин, слідів ступінчастого або нерівномірного зносу металу. За таких дефектів шайби треба замінити. На шайбах допускаються концентричні сліди приробітку з кулачками розподільчого валу.
49. Перевірте зазори між напрямними втулками та клапанами.
Зазори між клапаном та напрямною втулкою, мм:
- номінальний зазор для впускних клапанів …0,022-0,055
- номінальний зазор для випускних клапанів …0,029-0,062
- гранично допустимий зазор для впускних та випускних клапанів 0,3
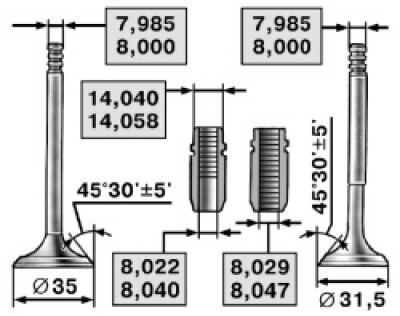
4.13. Розміри клапанів та їх напрямних втулок
Зазор обчислюється як різницю між діаметром отвору у втулці та діаметром стрижня клапана (Мал. 4.13).
Перевірку зазору рекомендується виконувати у спеціалізованій майстерні, тому що для вимірювання діаметра втулок потрібен спеціальний інструмент (нутромір).
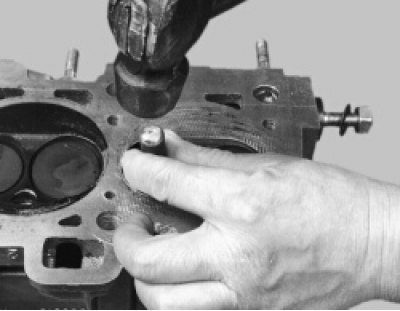
50. Якщо зазор не досяг гранично допустимого, можна спробувати усунути його заміною клапана. Якщо це не вдається або зазор перевищує гранично допустимий, замініть напрямну втулку. Для цього випресуйте з боку камери згоряння дефектну втулку спеціальною оправкою.
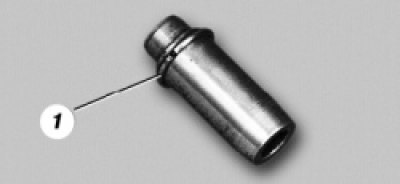
51. У запасні частини поставляються втулки зі стопорними кільцями 1. Зовнішній діаметр втулки збільшений, діаметр отвору під клапан зменшений.
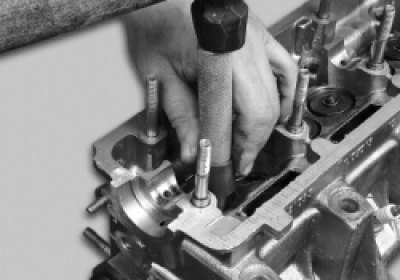
52. Змастивши втулку моторним маслом, вставте її в спеціальну оправку і запресуйте з боку розподільного валу до упору кільця стопорного в головку блоку. Розгорніть отвір у втулці за допомогою розгортки до 8,022-8,040 мм для впускних клапанів і до 8,029-8,047 мм для випускних.
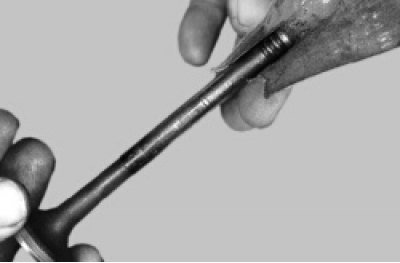
53. Якщо встановлюється старий клапан, зніміть задирки з проток під сухарі. Після цього необхідно притерти клапан до сідла [див. «Притирання клапанів» у підрозділі «Головка блоку циліндрів (ремонт)»].
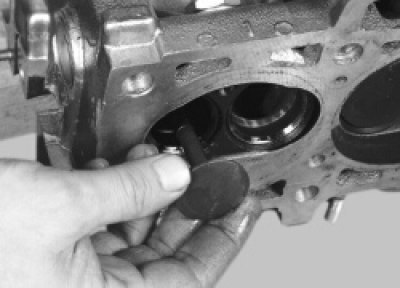
54. Встановіть клапани в головку блоку відповідно до попереднього маркування, попередньо змастивши їх стрижні моторним маслом.
55. Встановіть нижні пластини пружин клапанів.
56. Встановіть маслознімні ковпачки (див. «Заміна маслознімних ковпачків»).
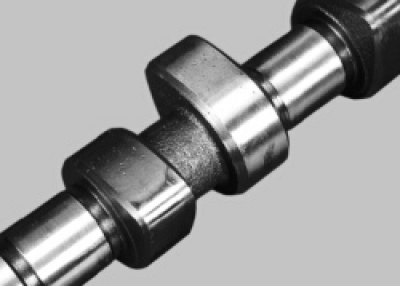
57. Замініть розподільний вал, якщо на його шийках і кулачках з'явилися сліди зношування, задираки та глибокі ризики. У майстернях, обладнаних спеціальними інструментами та пристроями, можна перевірити радіальне биття шийок розподільчого валу (воно не повинно перевищувати 0,02 мм) і зазор між отворами опор та шийками розподільчого валу, який не повинен перевищувати 0,2 мм (зазор для нових деталей 0,069-0,11 мм).
58. Встановіть розподільний вал та корпуси підшипників (див. «Заміна маслознімних ковпачків» у підрозділі «Заміна деталей ущільнення двигуна»).
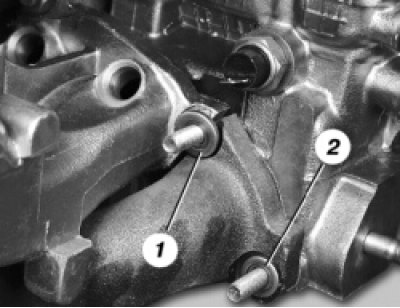
59. Встановіть прокладки, колектор та впускну трубу. Зверніть увагу, що під гайками (4 шт.), що кріплять одночасно впускну трубу та випускний колектор, встановлені шайби 1 більшого діаметру, ніж шайби 2 під рештою гайок…
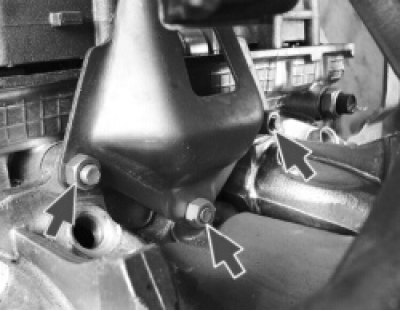
60. Під гайками кріплення кронштейна ресивера шайби не встановлюються.
61. Встановіть головку на блок циліндрів (див. «Заміна прокладання головки блоку циліндрів» у підрозділі «Заміна деталей ущільнення двигуна»), перевірте зазори у приводі клапанів і за необхідності відрегулюйте їх (див. «Регулювання зазорів у приводі клапанів»).